Aluminum is used for aircraft bodies because it is lightweight, has a favorable strength-to-weight ratio, is corrosion-resistant, and can be easily formed into aerodynamic shapes, contributing to fuel efficiency and overall performance.
Indeed, Materials play a critical role in the field of aviation, influencing the design, performance, and safety of aircraft.
While aluminum is still widely used in aviation, the trend toward composites is expected to continue as technology advances.
Ultimately, the choice of materials for aircraft bodies is dynamic, reflecting the industry’s pursuit of innovation and improvement.
Lightweight Superiority in Aviation:
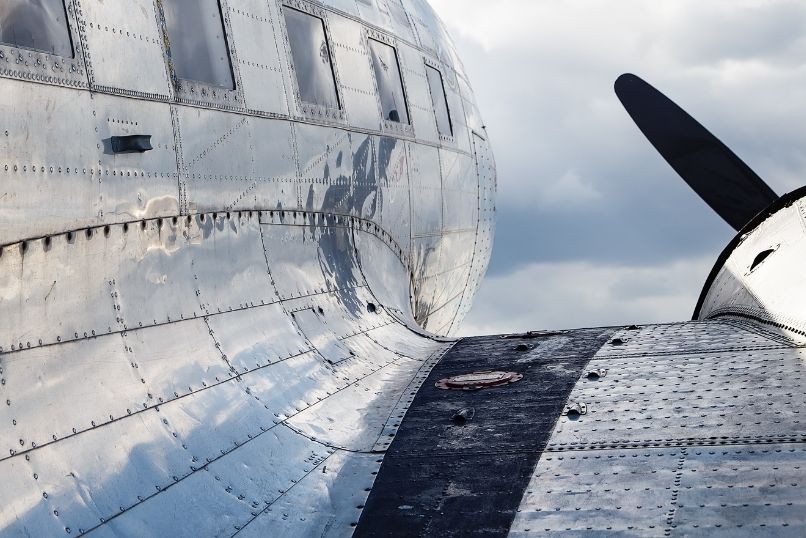
The aviation industry prioritizes lightweight materials due to their profound impact on aircraft performance, fuel efficiency, and overall operational capabilities.
The quest for lightweight superiority is driven by the fundamental principles of aeronautics, where minimizing weight translates to enhanced fuel efficiency, increased payload capacity, extended range, and improved overall performance.
Lightweight materials play a pivotal role in meeting the stringent demands of modern aviation, contributing to reduced operational costs and environmental sustainability.
Comparison of Aluminum’s Weight Advantages:
Aluminum has long been a stalwart in aircraft construction, primarily due to its favorable strength-to-weight ratio. The following points highlight the weight advantages of aluminum compared to alternative materials:
Strength-to-Weight Ratio: Aluminum alloys, especially those used in aerospace applications (e.g., 7000 series), offer a remarkable balance between strength and weight.
This property is crucial in aircraft design, where the goal is to maximize structural integrity while minimizing overall weight.
Density: Aluminum is a relatively low-density metal, making it lighter than many alternative materials.
This characteristic is essential for reducing the overall mass of the aircraft, leading to improved fuel efficiency and better performance.
Manufacturability: Aluminum is well-suited for traditional manufacturing processes like extrusion and machining, allowing for the production of complex aerospace components with a high strength-to-weight ratio.
The ease of fabrication contributes to cost-effectiveness and efficient manufacturing processes.
Corrosion Resistance: While aluminum is susceptible to corrosion, its alloys, when adequately treated or coated, exhibit good resistance.
This corrosion resistance is vital for ensuring aircraft components’ longevity and structural integrity, further justifying its use in aviation.
In summary, while aluminum has been a stalwart in aviation materials, the industry’s relentless pursuit of lightweight superiority has driven the exploration and adoption of advanced materials.
Strength-to-Weight Excellence in Aircraft Design:
The strength-to-weight ratio is a critical parameter in aircraft design, influencing the aircraft’s structural integrity, performance, and overall efficiency.
This ratio represents the balance between the material’s strength, ability to withstand applied forces, and weight.
In aviation, achieving a high strength-to-weight ratio is paramount because it allows for constructing robust structures without unduly increasing the overall mass of the aircraft.
Key Aspects of the Strength-to-Weight Ratio in Aircraft Design:
Structural Efficiency: The strength-to-weight ratio is a key determinant of structural efficiency in aircraft components.
A high ratio allows designers to create structures that are strong enough to withstand the aerodynamic forces and structural loads experienced during flight while simultaneously minimizing the weight of these structures.
Fuel Efficiency: Aircraft designers are constantly striving to improve fuel efficiency, and a higher strength-to-weight ratio contributes directly to this goal.
Reduced weight means lower fuel consumption, as the aircraft requires less energy to overcome gravitational and aerodynamic forces.
This is particularly crucial for long-range flights and contributes to aviation’s economic and environmental sustainability.
Payload Capacity: A high strength-to-weight ratio enables an aircraft to carry a more substantial payload without compromising safety or performance.
This is especially important for commercial aviation, where maximizing payload capacity directly impacts profitability.
Highlighting Aluminum’s Strength-to-Weight Excellence:
Aluminum has been a material of choice in aviation for decades, largely because of its exceptional strength-to-weight ratio. Here are key points highlighting how aluminum provides the necessary strength without compromising weight:
High-Strength Alloys: Aluminum alloys, such as those in the 7000 series, are specifically engineered for aerospace applications.
These alloys exhibit impressive tensile strength while remaining relatively lightweight. This allows for the construction of robust and durable aircraft structures.
Versatility in Design: Aluminum’s malleability and formability contribute to its versatility in aircraft design.
Corrosion Resistance: While aluminum is susceptible to corrosion, advanced surface treatments and coatings have been developed to enhance its resistance.
This corrosion resistance ensures the long-term structural integrity of aircraft components, contributing to their overall strength over the aircraft’s operational life.
Cost-Effectiveness: Aluminum’s affordability and the established manufacturing processes for working with it make it a cost-effective choice in aviation.
This is especially important for commercial aircraft production, where cost considerations are significant.
In conclusion, the strength-to-weight ratio is a pivotal factor in aircraft design, and aluminum’s ability to provide high strength without compromising weight has solidified its role as a primary material in the aerospace industry.
Corrosion Resistance in the Skies:
Aircraft operate in diverse environmental conditions, from the high-altitude, low-pressure atmosphere to exposure to varying temperatures, humidity, and precipitation.
These environmental challenges make corrosion a significant concern for aircraft bodies’ structural integrity and longevity.
Corrosion can weaken materials, compromise safety, and increase maintenance costs. In this context, the natural corrosion resistance of materials used in aircraft construction becomes a crucial consideration.
Aluminum’s Natural Corrosion Resistance:
Aluminum, a widely used material in aircraft manufacturing, possesses natural corrosion resistance that significantly contributes to the durability and reliability of aircraft bodies.
Several factors highlight aluminum’s effectiveness in combating corrosion:
Durability in Harsh Environments: Aircraft often encounter harsh environmental conditions, including exposure to saltwater, industrial pollutants, and acidic elements.
Aluminum’s resistance to corrosion makes it well-suited for these challenging environments, particularly in marine and coastal regions where salt corrosion is a common concern.
Low Maintenance Requirements: The natural corrosion resistance of aluminum reduces the need for extensive maintenance to combat corrosion-related issues.
This characteristic is particularly advantageous for the aviation industry, where minimizing downtime and maintenance costs is essential for operational efficiency.
Coating Compatibility: While aluminum exhibits natural corrosion resistance, additional protective coatings can be applied to enhance its performance in specific conditions.
Alloy Improvements: Advances in metallurgy have led to the development of aluminum alloys with enhanced corrosion resistance.
These alloys are designed to withstand even more challenging environmental conditions, making them suitable for critical aircraft components.
Formability and Aerodynamics
Importance of Aerodynamic Design in Aircraft Efficiency:
Aerodynamic design plays a pivotal role in the efficiency and performance of aircraft. Efficient aerodynamics minimize drag, enhance fuel efficiency, improve maneuverability, and contribute to overall operational effectiveness.
The shape and contours of an aircraft directly influence how it moves through the air, impacting factors such as lift, drag, and stability.
Optimized aerodynamics are crucial for achieving the best possible balance between speed, range, and fuel consumption.
How Aluminum’s Malleability and Formability Contribute to Aerodynamics:
Aluminum’s malleability and formability are key attributes that contribute significantly to the aircraft’s aerodynamic design. Here’s how these properties enhance the sleek and effective aerodynamics of aircraft:
Streamlined Shapes: Aluminum’s malleability allows it to be easily shaped into streamlined forms, which is essential for reducing drag.
Aircraft designers can craft smooth contours that minimize air resistance and turbulence as the aircraft moves through the atmosphere. This streamlining is crucial for achieving higher speeds and greater fuel efficiency.
Complex Curvatures: The formability of aluminum enables the creation of complex curvatures and contours that are precisely tailored to optimize aerodynamic performance.
Wings, fuselages, and other aerodynamic surfaces can be designed with precision to ensure efficient airflow, reduce lift-induced drag, and enhance overall stability.
Weight Efficiency: While primarily recognized for its strength-to-weight ratio, aluminum’s ability to be shaped into lightweight yet strong structures is equally important for aerodynamics.
By using aluminum in the construction of critical components like wings and fuselages, aircraft designers can achieve the desired structural strength without adding unnecessary weight, contributing to fuel efficiency and maneuverability.
Ease of Fabrication: Aluminum’s ease of fabrication supports the production of aerodynamically sophisticated components.
The material can be cut, stamped, and formed with relative ease, facilitating the manufacturing of intricate parts that contribute to optimal aerodynamic performance.
Integration of Components: The malleability of aluminum allows for the integration of various components, eliminating the need for additional seams or joints that could disrupt the smooth flow of air.
Thermal Conductivity for Peak Performance
Significance of Thermal Conductivity in Aviation:
Thermal conductivity is a crucial factor in aviation, influencing the performance and safety of aircraft components.
Aircraft encounter a wide range of temperatures during flight, from high temperatures at lower altitudes to extremely low temperatures at high altitudes.
Efficient heat dissipation is essential to prevent overheating of critical components, ensuring their reliability, longevity, and optimal performance.
Thermal conductivity plays a key role in managing heat generated by engines, avionics, and other systems.
Highlighting Aluminum’s Ability to Dissipate Heat:
Aluminum, a primary material in aviation, possesses excellent thermal conductivity properties that make it well-suited for dissipating heat from various components.
Here are key points highlighting aluminum’s effectiveness in managing heat in aircraft:
High Thermal Conductivity: Aluminum exhibits high thermal conductivity, allowing it to conduct and transfer heat away from critical components efficiently.
This property is essential for preventing the buildup of excessive heat, which can lead to component failure and compromise the aircraft’s overall performance.
Heat Sink Applications: Aluminum is often used for heat sinks, devices designed to absorb and dissipate heat.
Heat sinks are commonly employed in aircraft to cool electronic components, such as avionics and computer systems, preventing them from reaching temperatures that could adversely affect their functionality.
Weight Efficiency: In addition to its thermal conductivity, aluminum’s lightweight nature is advantageous for aerospace applications.
The use of aluminum in heat-dissipating components ensures that the added weight is minimal, contributing to overall fuel efficiency and aircraft performance.
Durability at High Temperatures: Aluminum remains structurally sound even under elevated temperatures, making it well-suited for components that are exposed to high heat from sources such as engines or other thermal stresses.
This durability is essential for ensuring the longevity of critical aircraft parts.
Ease of Manufacturing: Aluminum’s malleability and ease of manufacturing contribute to producing complex heat-dissipating structures.
Heat exchangers, for example, can be efficiently fabricated from aluminum to enhance thermal performance in various aircraft systems.
Sustainability and Recyclability
Environmental Impact of Material Choices:
Like many other sectors, the aviation industry faces increasing scrutiny regarding its environmental impact. Aircraft production, maintenance, and end-of-life disposal contribute to carbon emissions, resource depletion, and waste generation.
Therefore, adopting sustainable aircraft design and manufacturing practices is crucial for mitigating the industry’s environmental footprint.
Material choices play a significant role in these efforts, as the selection of materials with environmentally friendly properties can contribute to more sustainable aviation practices.
Emphasis on Aluminum’s Recyclability in Sustainable Aviation:
Aluminum stands out as a sustainable material choice in aviation, primarily due to its high recyclability. Here’s how aluminum contributes to sustainable aviation practices:
Endless Recyclability: Aluminum is 100% recyclable, and recycling does not degrade its quality or properties.
Unlike some other materials, which may experience downcycling (a reduction in quality with each recycling iteration), aluminum can be recycled indefinitely without
losing performance.
Reduced Raw Material Consumption: The recyclability of aluminum reduces the demand for primary aluminum production, thereby decreasing the need for extracting bauxite and the associated environmental impact.
Closed-Loop Systems: Adopting closed-loop systems, where aluminum from retired aircraft is recycled and used to produce new aircraft components, further enhances sustainability.
This approach minimizes waste, reduces the need for new raw materials, and contributes to a more environmentally responsible lifecycle for aircraft.
Lightweight Properties: Beyond recyclability, aluminum’s lightweight properties contribute to fuel efficiency, reducing the overall environmental impact of aircraft during operation.
Lighter aircraft require less fuel, resulting in lower emissions and improved operational sustainability.
Cost-Effectiveness in Production
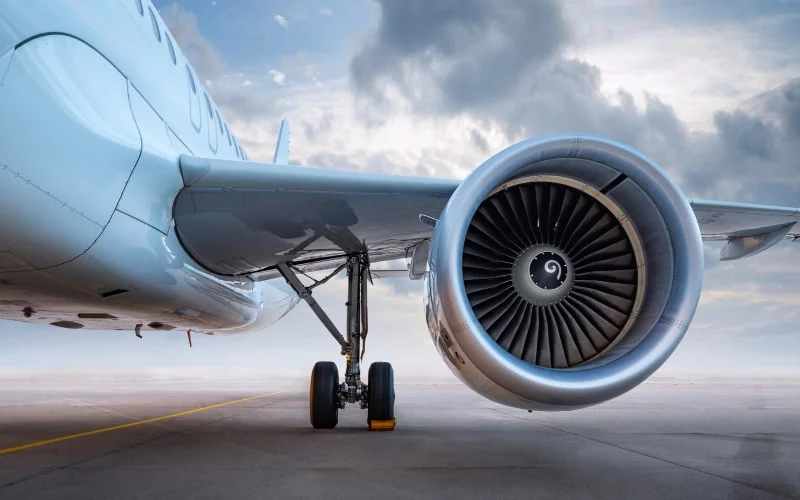
Overview of Economic Considerations in Aircraft Manufacturing:
Aircraft manufacturing involves complex economic considerations that directly impact the aerospace industry’s cost, efficiency, and competitiveness.
Several factors contribute to the economic landscape of aircraft production, including material costs, manufacturing processes, labor expenses, and the overall operational efficiency of the production facility.
Achieving cost-effectiveness is crucial for both commercial and military aerospace programs, as it influences aircraft’s affordability, market competitiveness, and profitability.
Why Aluminum is a Cost-Effective Choice:
Aluminum’s popularity in aircraft manufacturing is driven by several factors that contribute to its cost-effectiveness:
The relatively low cost of extracting and processing bauxite into aluminum makes it an economically attractive raw material for aircraft construction compared to some alternative materials.
Ease of Fabrication: Aluminum is highly malleable and easily fabricated using common manufacturing techniques such as extrusion, forging, and machining.
The ease of working with aluminum contributes to streamlined and cost-effective production processes.
The material’s formability allows for the creation of intricate, lightweight structures without the need for complex manufacturing methods, reducing production time and costs.
Established Manufacturing Infrastructure: The aerospace industry has a well-established infrastructure for working with aluminum, including extensive experience, standardized processes, and readily available manufacturing equipment.
This familiarity and infrastructure contribute to cost-effectiveness by minimizing the need for new investments or extensive retooling when using aluminum in aircraft production.
Weight Efficiency and Fuel Savings: Aluminum’s favorable strength-to-weight ratio supports the design of lightweight yet structurally sound aircraft.
The resulting reduction in weight contributes to improved fuel efficiency, which is a significant economic consideration over the operational life of an aircraft.
Lower fuel consumption translates into cost savings for airlines and operators.
Recyclability and Sustainability: The recyclability of aluminum is not only environmentally advantageous but also economically beneficial.
Incorporating recycled aluminum into aircraft manufacturing reduces the demand for primary aluminum production, which typically involves higher energy costs.
This closed-loop approach aligns with sustainability goals and can contribute to cost-effectiveness in the long term.
Proven Track Record: Aluminum has a long and successful track record in aviation, having been used for decades in various aircraft models.
The reliability and performance of aluminum components contribute to lower maintenance costs and overall operational efficiency, enhancing the economic viability of aluminum in aircraft construction.
Looking Forward: Innovations and Alternatives
Looking Forward: Innovations and Alternatives in Aircraft Design:
The aviation industry is at the forefront of ongoing research and development, continually exploring innovative materials and technologies to enhance aircraft performance, efficiency, and sustainability.
Several emerging trends and alternatives are shaping the future of aircraft design:
Advanced Composite Materials: While aluminum remains prevalent, advanced composite materials, such as carbon-fiber-reinforced polymers (CFRP) and other high-performance composites, are gaining prominence.
These materials offer superior strength-to-weight ratios, allowing for lighter and more fuel-efficient aircraft structures.
Bio-based Materials: Researchers are investigating bio-based materials derived from sustainable sources, such as plant fibers or bio-resins, to reduce the environmental impact of aircraft manufacturing.
These materials aim to combine lightweight properties with eco-friendly sourcing.
Additive Manufacturing (3D Printing): Additive manufacturing techniques, including 3D printing, transform how aircraft components are produced.
This technology enables the development of intricate and lightweight structures, potentially leading to decreased material waste and manufacturing costs.
Lightweight Metals: Beyond aluminum, other lightweight metals like titanium and magnesium are being explored for their potential in aircraft design.
These metals offer different combinations of strength and weight characteristics, providing designers with more options to optimize performance.
Hybrid-Electric and Electric Propulsion: Advances in electric propulsion systems and hybrid-electric aircraft designs aim to reduce emissions and increase energy efficiency.
Nanomaterials and Nanotechnology: Nanomaterials and nanotechnology are being explored for their potential to enhance material properties, such as strength, conductivity, and durability.
FAQs
Why is aluminum preferred for aircraft bodies?
Aluminum is preferred for aircraft bodies due to its combination of strength and lightweight, making it ideal for constructing structures that need to be both sturdy and lightweight.
What specific properties of aluminum make it suitable for aircraft construction?
Aluminum possesses a high strength-to-weight ratio, excellent corrosion resistance, and good formability, allowing for the fabrication of complex aircraft structures while keeping weight to a minimum.
Are there different types of aluminum alloys used in aircraft manufacturing?
Yes, various aluminum alloys are utilized in aircraft manufacturing, such as the 2000 and 7000 series, which offer specific advantages in terms of strength, durability, and fatigue resistance.
Is aluminum susceptible to corrosion, and how is this addressed in aircraft design?
While aluminum can corrode, aircraft manufacturers use corrosion-resistant alloys and employ protective coatings to mitigate corrosion risks and ensure the aircraft’s longevity.
How does aluminum compare to other materials, such as composites, in aircraft manufacturing?
Aluminum is still widely used due to its proven reliability and cost-effectiveness. However, composites are gaining popularity for specific applications due to their higher strength-to-weight ratio and corrosion resistance.
Are there advancements in aluminum technology for aircraft bodies?
Yes, ongoing research aims to develop new aluminum alloys with improved strength, fatigue resistance, and other properties to enhance the performance and efficiency of aircraft structures.
How is aluminum used in the construction of modern commercial airplanes?
Aluminum is extensively used in airframe construction, including the fuselage, wings, and other structural components. It provides the necessary balance of strength and weight to meet the demanding requirements of commercial aviation
Conclusion
The aviation industry faces a dynamic future marked by ongoing innovation in materials and technologies.
While aluminum continues to be a stalwart in aircraft manufacturing, emerging materials such as advanced composites, bio-based alternatives, and innovative technologies like additive manufacturing are shaping the next generation of aircraft design.
As the industry strives for enhanced sustainability, efficiency, and performance, the commitment to research and development remains a driving force, promising a future where aircraft are safer, more efficient, and more environmentally friendly.